Au milieu des années 60, plusieurs fabricants étaient à la recherche de nouveaux outils ou systèmes capables de reprendre le traitement de petites balles de foin et de paille et d’économiser ainsi du temps. L’un de ses fabricants était l’entreprise Hesston du Kansas, aux Etats-Unis. En 1966, l’ingénieur Hesston Keith Garrison a fait développer une machine pour la collecte de paille ou de foin sans pistons ou système de nouage compliqué. Il fallait toutefois une machine capable de compacter le produit ramasser. Le résultat: le Hesston Stakhand, une autochargeuse introduite en 1969.
Compacter verticalement de 4 à 7 fois par stack
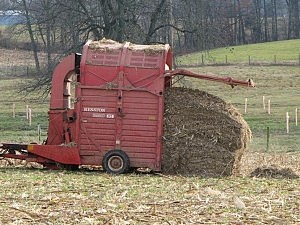
Contrairement à la concurrence, telle que New Holland, Freeman et Farmhand, qui avaient développé une remorque autochargeuse de balles permettant de former des piles (ou stacks) de foin ou de paille à base de ballots, Hesston Stackhand avait un tout autre fonctionnement. L’andain de foin ou de paille était ramassé par un axe avec quatre rangées de fléaux. Ces fléaux créent une aspiration qui permet de souffler le produit dans la caisse. Lorsque la caisse était remplie, on arrêtait le ramassage. Via une corde, le chauffeur activait deux vérins hydrauliques double effet qui poussaient le tout vers le bas afin de compresser l’herbe ou la paille. Une action relativement rapide qui ne demandait pas plus de 15 à 20 secondes.
Aux Etats Unis, les meules à foin étaient souvent stockés dehors, c’est pourquoi le dessus du Stackhand avait la forme d’un toit de mansarde afin d’éviter qu’il pleuve à l’intérieur. Lorsque le toit était relevé, on continuait le ramassage du produit dans l’andain. Le pressage se faisait de quatre à sept fois, après quoi la meule de foin (stack) était prête et pouvait être déchargée. La porte arrière avec une charnière au-dessus, qui pouvait être reliée au toit du Stackhand via un reliage mécanique. En soulevant le toit, la trappe arrière était ouverte en position horizontale. La chaîne de fond avec ameneurs poussait la meule à foin vers l’extérieur en continuant doucement à rouler. La densité de presse de la meule à foin s’accordait environ à celle d’une presse à densité moyenne de l’époque: bien plus haute que chez des autres marques de stackers de foin ou de paille.
Une pompe et un réservoir à huile alimentés par une prise de force étaient montés sur la machine pour l’alimentation et les commandes du système hydraulique?
Stackhand 10
Le Hesston Stackhand n’était initialement livrable que dans une version faisant des tas de 6 tonnes. Un Stackhand plus petit, qui faisait 10 à 30 meules de foin de 1 et 3 tonnes, ont rapidement suivi. Aux Etats Unis, le Stackhand 10 était utilisés avec succès dans des élevages devant presser 100 tonnes par an. Les stacks ou meules à foin compacts du Stackhand 10 pesaient plus de 1250 kg en foin. Le Stackhand 10 atteignait une capacité de 4 à 6 tonnes par heure. De plus, le Stackhand pouvait collecter de la paille de maïs ou de haricots, ce qui permettait d’amortir la presse plus rapidement. Aux Etats Unis, les stacks étaient presque toujours stockés en plein air près des étables. L’inconvénient de ce stockage bon marché était que les stacks s’ouvraient par temps venteux. Ceci les rendait difficiles à déplacer.
Stackhand 10 et préfané
En 1972, Timmerman & Verbeek BV (Pays-Bas), une filiale de Cebeco Handelsraad, décidait d’importer le Hesston Stackhand 10 en réponse à la méthode d’ensilage avec autochargeuses à la popularité croissante à l’époque. Vu que le Stackhand 10 était développé pour le ramassage de paille et de foin, Timmerman & Verbeek promouvait l’utilisation du système Stackhand pour le ramassage et la compression de préfané. En 1973, deux entrepreneurs agricoles ont entamé le travail avec le Stackhand. Les piles avaient des longueurs de 2,40m, des largeurs de 2,10m et des hauteurs de 2,40m. Le poids d’un stack était d’environ 1500 kg à 50% de matière sèche. La capacité quotidienne du Stackhand 10 était de 5 à 6 ha par jour. Les piles étaient mises dans la direction de la longueur deux par deux avec un Stakmover ou un pince à foin au relevage à trois points, afin de former une sorte de silo. Les deux meules à foin, placés l’une contre l’autre, étaient ensuite couverts de plastic et de terre pour une bonne conservation. Des recherches au ILR de Wageningen ont démontré qu’à 50% de matière sèche du produit, le mètre cube de produit brut ne comportait 75-120 kg de matière sèche, ce qui augmentait fortement les chances de fermentation. En comparaison avec un ensilage de l’époque, le poids par mètre cube de matière sèche était de plus de 160 kg. Pour nourrir, les meules à foin étaient prises sur un chargeur arrière.
Bien que l’Hesston Stackhand 10 coûtait environ 12.000 euro en 1974, c.à.d. plus de 4000 euro de plus qu’une autochargeuse, TImmerman & Verbeek a vendu 26 Hesston cette année-là. L’avantage du Stackhand était qu’un entrepreneur agricole pouvait effectuer le ramassage, le pressage et le déchargement tout seul. Toutefois, la presse autochargeuse perdit rapidement en popularité en Europe par rapport à l’ensilage et le pressage de préfané. Le système requérait plus de plastic, et surtout l’utilisation de bâches de protection augmentait vu que couvrir une forme irrégulière était plus difficile que de couvrir un silo.
Aux Etats Unis, par contre, le Stackhand demeurait très populaire, surtout dans les années 70 et début années 80. La machine a même causé une procédure juridique entre Hesston Corporation et Deere & Company. John Deere avait entamé la production de trois modèles de Hay Stack Wagon en 1974. Un concept basé en grande partie sur le Stackhand de Hesston, malgré le fait que Hesston était le titulaire du système Stackhand. Une notion contestée par John Deere, qui affirmait que le brevet n’était pas valable. La cour de justice en a cependant décidé autrement et jugé en faveur de Hesston. Peu après le jugement, Deere a stoppé la production des Hay Stack Wagons.
Quant à Hesston, la production du Stackhand s’arrêtera en 1985, la ligne d’assemblage ainsi libérée étant reprise pour la production de presses à balles rondes et à grandes balles.
Texte: Jan Ebinger IMAGES: Jan Ebinger & Farmphoto